Sortation is one of the most vital functions of a warehouse. It seems straightforward, but the nuance behind a solid sorting system is the difference between fast order turnover and shipping delays. Speed is the key factor that customers are demanding. They want their orders to arrive sooner without any additional costs, which has forced fulfillment providers to adapt. In this article, we will define sortation, show where it is used, and provide tips to help improve your sortation process.
What is Sortation?
Sortation is the process of organizing and separating items in a way that makes it easier to store, pick, and ship. It can also be referred to as “sorting.” and it’s extremely important for ensuring inventory accuracy and efficiency.
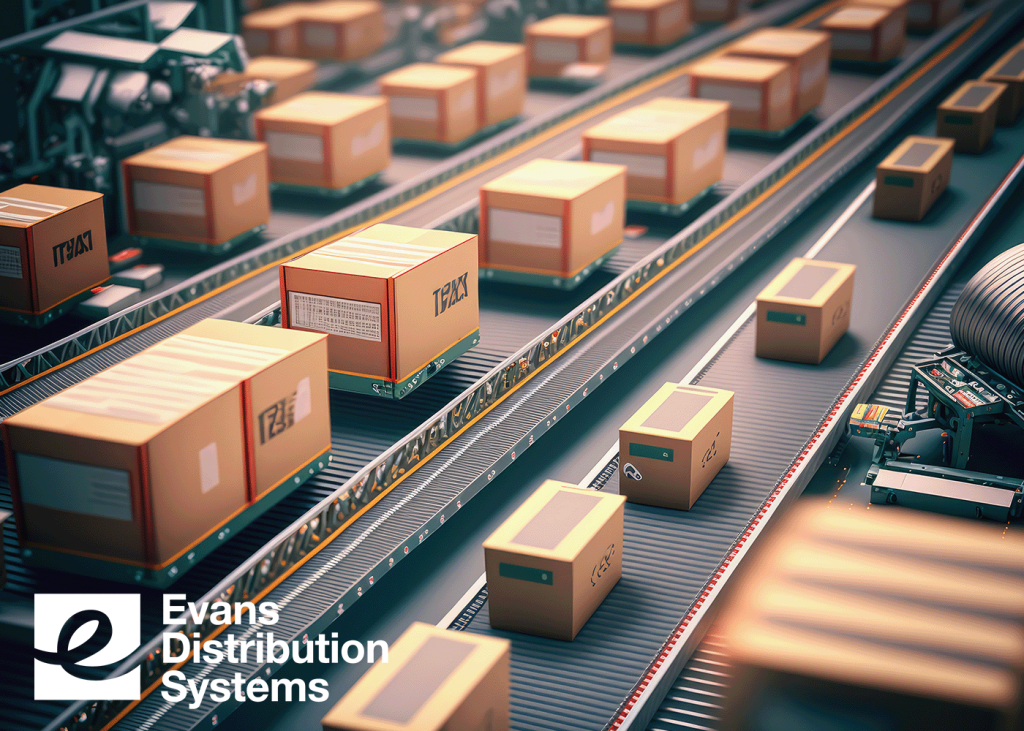
The Sortation Process
The sortation process encompasses multiple steps of the fulfillment process. It begins with a barcode system and a clearly defined warehouse layout. Barcodes allow warehouse associates to update the warehouse management system (WMS) of the product’s location and its receipt or shipment status.
When a product arrives for storage, it is labeled and entered in the WMS. It is then relocated from the receiving area and put away in its designated place. The barcode is scanned, and the inventory is updated in the system.
When an order is received, a warehouse associate is tasked to build it. The items are picked from warehouse inventory and packaged together. Once the items are picked and packed, the order gets sorted based on the applicable shipping method and location of delivery. In a high-volume fulfillment sortation process, packages may be sorted based on size, weight, package type, or carrier.
Technology
Although human labor is still vital for warehouse operations, new sortation technology allows businesses to keep up with order volumes in a way that wouldn’t have been possible before. New forms of RFID scanning technology can scan packages on the conveyor system and have them diverted to the correct staging area. These scanners can also be used on dock doors to update the WMS when the product moves in and out of the warehouse.
The many different conveyor systems fall into two main categories. First, are systems where lines from multiple sources are merged into a single stream. A good example of this would be a sliding shoe sorter. Second, are systems that run in a continuous loop. These systems have products added in one section and the conveyor delivers those items to specific areas for order building. A good example of this system would be the push-tray sortation system. The best technology for any individual operation will depend on the size of the warehouse, order volume, and items being sorted.
Tips to Improve the Sortation Process
Now that we understand the sortation process and its importance, we will identify the areas that can be optimized for the most improvement. By improving specific touch points in the process, we can optimize the entire system.
Use the Right Picking Strategy
Depending on the size of the operation and order volume there are four main picking methods that can be used. When selecting a picking strategy, you’ll need to consider the warehouse size and layout, order volume, and number of employees available. A small operation may use a piece-picking strategy whereas a large operation with high order volume would likely use zone picking.
Reduce the Walking Distance
Where is the product stored in relation to where it is packed? As business picks up and order volumes increase, products should be stored closer to the packing area. This will help reduce the time traveling in the warehouse to pick the order and allow for higher order capacity. Store the most popular items closest to the packing area when possible.
Update Your Warehouse Management System
An updated WMS can help you identify bottlenecks in the process and provide real-time data as orders come in. It can track on-hand inventory, shipment data by SKU, average turn rate, and much more. Comparing order processing time to SKU location will ensure the optimal sorting process. Evans uses WMS data to create business intelligence dashboards in the evans365 customer portal to optimize its operation and provide account visibility to customers.
Customize the Conveyor Systems
If a conveyor system is used in the sorting process, then it’s important to ensure the system works well with the warehouse space. Most systems are customizable and are compatible with each other. Different conveyor systems can be used at varying stages of the sorting process. Customizing the conveyor system ensures speed and efficiency.
Implement Automated Tools
We are living in the age of automation and modern sortation systems are the proof of that. Motion sensors, bar-code scanners, visual AI systems, and robots have automated the sortation process. Using automated tools instead of manual labor for tasks such as sorting will free up employees to do tasks that can’t be automated. Simple tasks like moving items from a storage area to the picking area or checking order accuracy can be automated to improve the sorting process.
Conclusion
Sortation plays a vital role in warehousing and fulfillment by ensuring orders are built quickly and accurately. The emergence of new technologies and automation has increased customer expectations for faster shipping. Utilizing the proper sortation system will help companies to improve shipping speeds and increase customer satisfaction.